How to Accurately Prepare a Bill of Materials (BOM) List
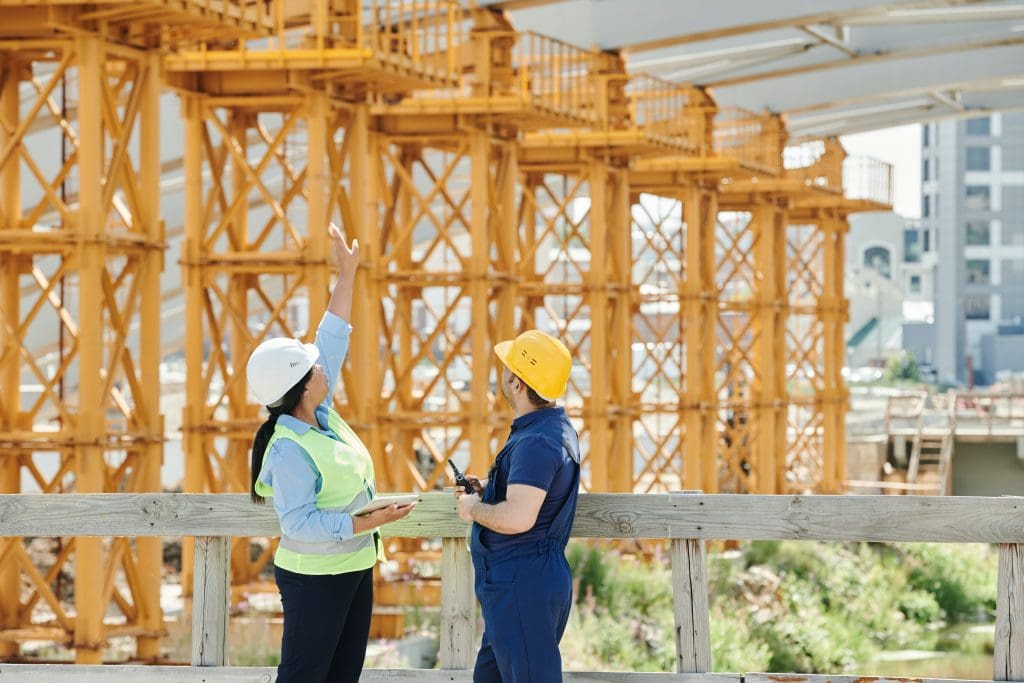
Creating a Bill of Materials (BOM) list is an integral part of the scaffolding planning and bid process. It helps to ensure your business has all the materials and components required to construct a scaffold.
In other words, it assists you in preventing inventory inaccuracies, wastage, and construction delays, which can cost you both time and money.
Given that construction materials prices are at an all-time high due to rising demand and the disruption caused by COVID/Brexit, this means that you should definitely know how to accurately prepare a Bill of Materials list.
In this article, we will dive deep into the meaning of BOM, why it matters, and how to accurately prepare one, especially with the help of software. This will help you deliver top-notch scaffolds to your customers in a timely and efficient manner.
What Is a BOM?
A BOM is a detailed list displaying all materials and components needed to construct a scaffold. This includes the quantity of parts, total weight/volume, and netting area based on the design of your scaffold. In short, it is the foremost step you take to build a scaffold.
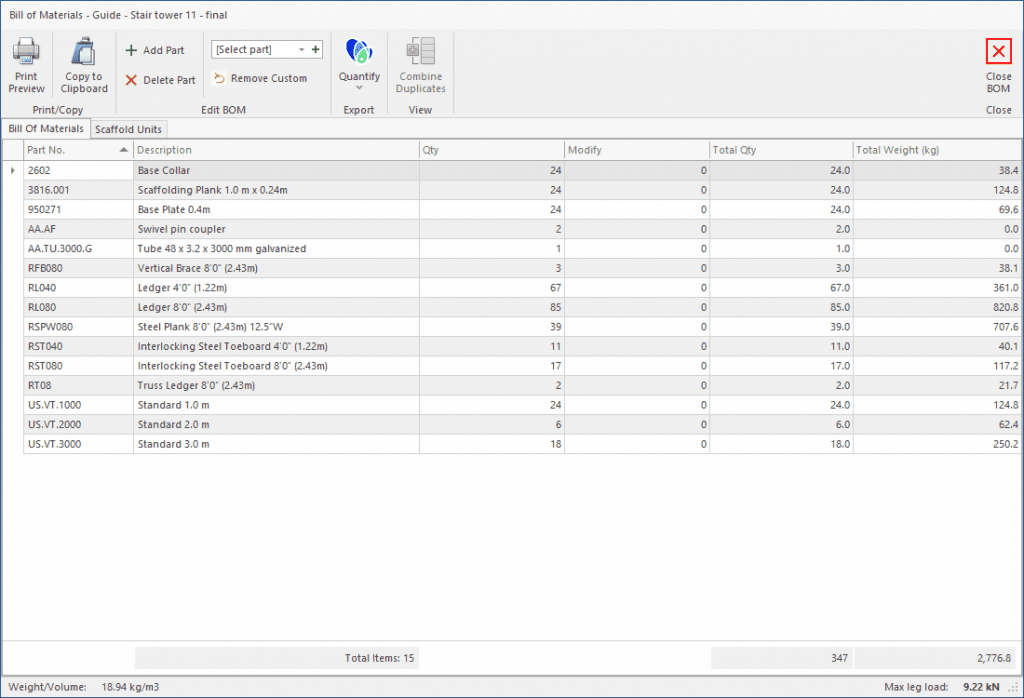
With an accurate BOM, it will be easier for your company to plan purchases of materials, estimate costs, manage inventory, and minimize production delays and waste. Although the concept of creating a BOM is straightforward, the goal is to create an accurate one to ensure you don’t face any hiccups during the construction phase, especially if your scaffold design is complex.
Who Creates a BOM?
In the scaffolding industry, the responsibility of preparing a Bill of Materials can fall to several individuals such as supervisor, contracts manager, designer, or engineer.
Seven Items to Include in an Effective BOM
Coming up with an accurate BOM list requires you to include specific information and in-depth data. Without those, you may not be able to successfully build scaffolds with minimal errors. Over time, inaccurate data can also affect the decision-making process in your company. To help you out on this, here are some essential elements that you should include in a BOM list.
BOM Level
This illustrates the overall number or ranking of assembly and parts included in a broader BOM. By assigning a BOM level, you can organize the list to see all relevant parts at all levels including cost, size, and production time.
Part Name
This indicates the name of each part, material, or assembly for the creation of a scaffold. It’s important to assign a name for all these components as it helps users to identify the parts quickly, without needing to cross-reference with other sources.
Part Number
Just like part name, each item within the BOM must be given a unique part number for easy identification for everyone who is assessing the BOM.
Description
It’s vital for you to include a comprehensive and informative description for each material or part within a BOM. A detailed description helps you and others identify parts and discern similar parts and materials.
Quantity
Fill in the number of parts to be used in each assembly, subassembly, or disassembly to help guide you in the purchasing and manufacturing decisions.
Unit of Measure
Ensure all parts included in a BOM come with country-specific measurement units such as lbs or kg, ft or m. Be consistent across all similar part types because the information will help ensure the right quantities are acquired and delivered for the construction of scaffolds.
BOM Notes
Include any other relevant notes or supporting documentation to keep everyone assessing your Bill of Materials on the same page.
Why Is an Accurate BOM Important?
An accurate BOM not only helps you to identify all materials and components required to construct a scaffold, but it can also determine whether you have everything you need to move forward with the project with minimal risk of delays while still staying within the budget.
Additionally, a BOM also gives all stakeholders a sense of transparency as they know what items are needed during different stages of construction.
A BOM is also particularly useful for inventory management and purchasing teams as they will be able to purchase the right amount of materials at the right time to avoid unnecessary wastage.
Create Accurate BOMs with Avontus Designer®
While organizations manage their Bill of Materials in spreadsheets, there are several reasons why you shouldn’t. Some of the reasons include poor security, prone to inaccuracies, and difficulty integrating with other systems.
Based on these limitations, leveraging a software solution to generate a BOM list may be a smart move.
In fact, according to an industrial report by Avontus, 64% of surveyed respondents want scaffold design software with an instant material calculation feature.
Let us introduce you to Avontus Designer®. It allows you to instantly generate a BOM list based on your design, add or modify quantities, and accurately measure or count various scaffold metrics.
The software also comes with a Material Master, a complete database of stock materials for each supported system, which can be customized to match the available materials from your suppliers or within your own inventory.
AutoCAD users can also generate accurate BOM using our Avontus Counter add on. You can instantly count materials based on your design, customize your inventory, and export reports and graphs to Excel, Word, or PDF format for easy sharing.
Learn more about Avontus Products now and create an accurate BOM list in a breeze!